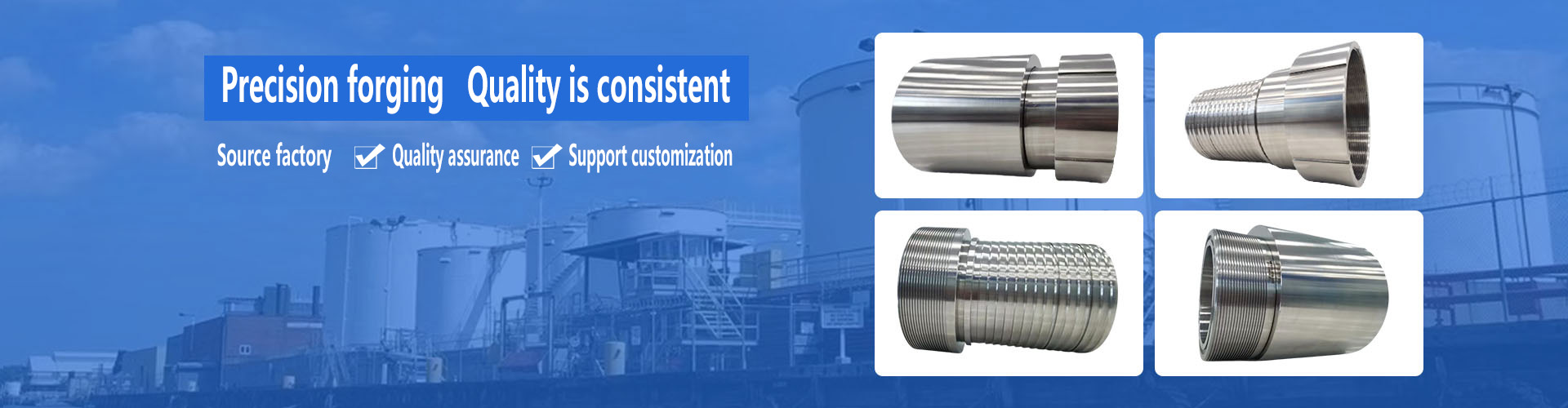
The titanium tube manufacturer will explain to you the problems and repair methods encountered during titanium tube welding:
Pores are a common problem encountered during titanium tube welding. The fundamental reason for the formation of pores is due to the influence of hydrogen. The formation of pores in the weld metal mainly affects the fatigue strength of the joint. Hydrogen is the main cause of cold cracking and pore formation. Because hydrogen is below 300 ℃ α The solubility in the phase is very low, with a solubility of only 0.002% at room temperature. When the weld seam or heat affected zone is cooled below 300 ℃ after welding, supersaturated hydrogen is converted into titanium hydride( γ Precipitation in the form of phases.
The increase in volume generates intergranular stress, which can lead to intergranular microcracks. Under external stress, intergranular microcracks can propagate into cracks. When welding titanium pipes, the possibility of thermal cracks occurring in the welded joints is very low. This is because the impurity content of S, P, C and other impurities in the titanium pipes is very low, and the low melting point eutectic formed by S and P is not easy to appear at the grain boundaries. In addition, the effective crystallization temperature range is narrow, and the shrinkage during solidification of titanium pipes is small, so the weld metal will not produce thermal cracks. However, during titanium tube welding, cold cracks may appear in the heat affected zone, characterized by cracks occurring several hours or even longer after welding, known as delayed cracks. During the welding process, hydrogen diffuses from the high-temperature deep pool to the lower temperature heat affected zone. The increase in hydrogen content increases the amount of TiH2 precipitated in this zone, increasing the brittleness of the heat affected zone. In addition, due to the volume expansion of hydride precipitation, significant structural stress is caused, and hydrogen atoms diffuse and aggregate towards the high stress areas of this zone, resulting in the formation of cracks.
When welding materials such as titanium pipes, when the temperature is above 500-700 ℃, it is easy to absorb oxygen, hydrogen, and nitrogen in the air, which seriously affects the welding quality. Therefore, when welding titanium alloys, strict protection must be applied to all aspects of the melt pool and the weld zone in high-temperature areas (above 400-650 ℃).
Therefore, special protective measures must be taken during the welding of titanium pipes. Therefore, the method of argon arc welding is adopted for treatment, and a larger welding torque is sprayed to expand the area of the gas protection zone. When the nozzle is insufficient to protect the weld seam and high-temperature metal near the seam, an argon protection drag cover needs to be added.
Correctly select welding process parameters to remove organic substances such as oxide skin and oil stains on the surface of the welded parts and welding wires. Control the flow rate and velocity of argon gas to prevent turbulence and affect the inflation protection effect. The method of using manual tungsten inert gas arc welding to treat cracks in titanium alloy welding is feasible and can achieve satisfactory results. The pre welding preparation and groove selection are:
(1) Selection of welding materials. The purity of argon gas should not be lower than 99.99%, the dew point should be below -40 ℃, and the relative humidity should be less than 5%. When the pressure in the argon cylinder drops to 0.981 MPa, it should be stopped from use. The filling wire is generally made of homogeneous materials. To improve the plasticity of the joint, TC3 welding wire can be used, which has a slightly lower alloy degree than the base material. TC3 welding wire is used for this welding.
(2) The surface quality of welded parts and welding wires has a significant impact on the mechanical properties of welded joints. Before welding, the test piece and welding wire can be pickled first. Rinse with clean water, dry and immediately apply welding. Use acetone, ethanol, carbon tetrachloride, methanol, etc. to wipe the titanium plate groove and the parts on both sides (within 50mm), the welding wire surface, and the tool clamp in contact with the titanium plate.
(3) Selection of welding equipment. Titanium tube argon arc welding should use a DC argon arc welding power source with descending external characteristics and high-frequency arc ignition, and the delay gas delivery time should not be less than 15 seconds to avoid oxidation and pollution during welding. So WSM-315 IGBT inverter DC pulse argon arc welding machine is adopted.
(4) The selection of groove form. In principle, try to reduce the number of welding layers and welding metal as much as possible. As the number of welding layers increases, the cumulative suction amount of the weld seam increases, which affects the performance of the welded joint. Due to the large size of the welding pool during titanium pipe welding, a V-shaped 70-80 ° groove is required for the welded part.